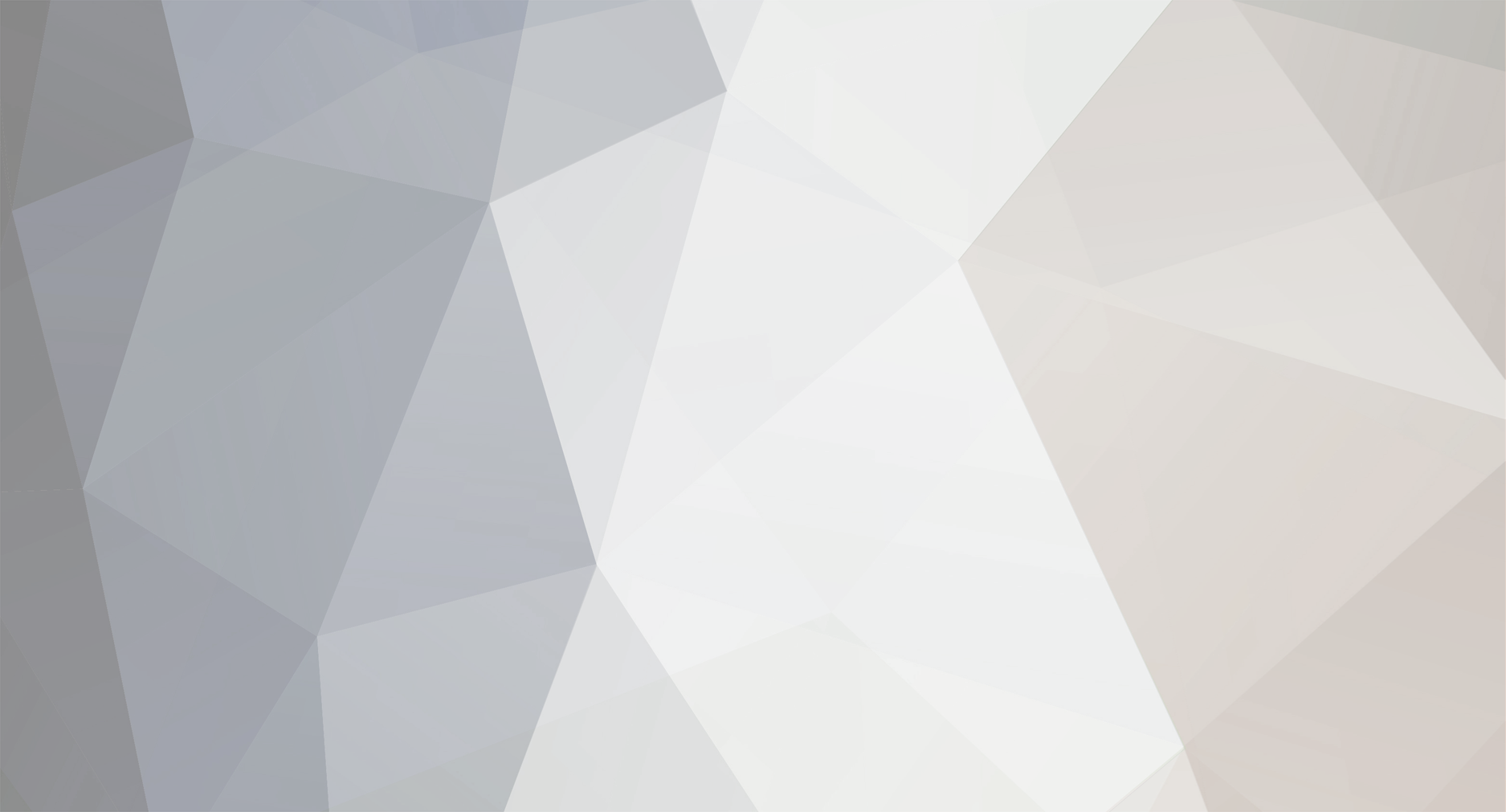
WR1
Administrator-
Posts
985 -
Joined
-
Last visited
-
Days Won
286
Content Type
Profiles
Forums
Events
Everything posted by WR1
-
Well its not a mistake, its just a method.
-
Can We Reduce F11=F12=F22=0.25 In Designing Slabs
WR1 replied to mhdhamood's topic in Concrete Design
no you dont need to reduce anything -
Major Update
WR1 replied to UmarMakhzumi's topic in Website Announcements/ Problems/ Login/ Registration Issues
I am eager for this. -
Slenderness Ratio Check For Columns By Etabs
WR1 replied to Muhammad Sohail Khan's topic in Concrete Design
First of all how do you know that your structure is braced/unbraced and moment magnification will not be applied? Second thing sir baz, can we over-ride minimum eccentricity according to code provisions? -
1000Kn is perfectly normal! if i am perceiving correctly his project.
-
Yes Shaker you are right. I have done this in a project intensely (although i believe the temperature values we apply in ETABS are unrleastic for example delta T=20-30C which is too high in my opinion). Anyway we used the same values. Yes tension, compression force will be so high. Dont forget the compression, if you are designing for 1000KN tension then also design for 1000KN compression. The easy method is to define these beams as columns in ETABS (P-M-M) design instead of just flexural design as in beams. As Mr. Baz pointed out, these will be designed for combined axial and flexural loads. Another easy thing is to design for flexure only and then add area of steel for axial force which T=Ast.fy.phi (This will give more steel as compared to combined axial+flexural design). A conservative approach (A lazy person approach). So far so good for strength design. But when it comes to cracking and serviceability design, for example imagine above ground huge water tanks with these axial forces, life does not look so easy in that case.
-
great book. well some suggestions from my end Mastery by Robert Greene Why A students work for the C students and B students work for the government Negotiate This by Herb Cohen Dealing with people, power and politics at work The Girl You Left Behind
-
Just to add, There could be drops in any shape or at any location in a slab, you just design for it. The effective depth will increase ofcourse for thicker slabs. I would preferably not design such slabs as cantilever on supported by the other slab, rather I will design it as continuous. The portion where two slabs meet, I will consider it as beam and provide side bars for torsion.
-
R factor is used to account for expected ductility of building in earthquake loading. There is no R in non-linear analysis. Lesser R means less post-yield ductility and hence more base shear and vice versa. If a building is ductile (more R) we design for less base shear because in reality building has considerable ductility even after yielding (energy dissipation in non linear range) so in simple words lets say the actual seismic force in reality is 100kn then in linear elastic code based design we design it for only 50kn (hypothetical) and for the remaining 50kn we assume based on structural framing system that building will resist by post-yield ductility. Most common lateral resisting systems are moment frame system, shear wall system, building frame system, flat slabs (not in higher seismic zones) etc. You first determine seismic design category and see limitations on type of lateral system you can "assume" to find R.
-
check for the pressure under all combinations including lateral loads. in SAFE 12 onwards, uplift (tension) will be with positive sign (blue colors by default) and in SAFE 8 it will be negative.
-
they can be..why not? but you have to design them accordingly.
-
It is very unfortunate that there is no general public education/awareness about eqs in Pakistan. Nor is there any "effective" disaster control management.
-
In addition to what Uzair said, a conservative shortcut would be to apply 1.5kPa load as wind pressure.
-
Construction Materials Used In Faisal Mosque
WR1 replied to Muhammad Nakhshab Ajaz's topic in Students Zone
Concrete! isnt it?- 2 replies
-
- materials
- construction
- (and 8 more)
-
· Concept of structural stresses based on linear finite element method (FEM) If I understand it properly then you are seeking basic concepts, like how to calculate stresses by using FEA, For this you can read any basic book, university notes. For example, the book by Robert D Cook. Search in this forum you will find other related posts too. · Static assessment based on non-linear FEM · Fatigue assessment based on stress and strain calculations · Fracture mechanics to determine crack growth Rest of these topics are advance. And I have never worked in these areas. I am not sure whats your level in FEA but if you are a beginner then it should take a lot of time in the first step above before you can move on!
-
just check the base reaction from DL and LL you seismic weight will be DL+0.25LL
-
Thats not a beam, its just a local stiffening, it will bend with the slab. You should design the whole panel as one with all sides resting on walls. You are going to have huge deflections as its simply supported on very stiff walls with no continuity! Think about hordi/waffle slab system if columns cannot be provided. 4 inch finishes? thats huge!
-
You should read about in ASCE code or text books like "Reinforced Concrete Design of Tall Buildings by Bungale"...
-
Yes you need to check each member, if axial force is more than the limits in code, you design it by P-M-M interaction (like column design) other as beam design (only for 1 direction moment + torsion + shear). But as Muneeb said, you can have an idea what type of loading is and what forces are experienced by members.
-
Which Civil Discipline Would You Pursue After Bachelors
WR1 replied to Ayesha's topic in Students Zone
let me know about this...this is MY field- 13 replies
-
- materials
- hydraulics
-
(and 6 more)
Tagged with:
-
SAP/ETABS/SAFE reports 3 values of shear reinforcement by default. These are 3 segments along the length of beam. From where this number 3 comes? This is called the station spacing. By default the max station number is 3 (beam is divided in 3 equal parts). For each part software reports reinf design values.
-
just divide both beams at intersection with no releases
-
Many engineers are confused with stiffness modifiers stuff in ETABS including me. Let me add my cent here. 1. Any reasonable set of stiffness can be used as explained in ACI 318. 2. You have to determine what type of frame you are analyzing; braced or un-braced 3. Whats the analysis type? Strength, service? 4. Code allows use of 0.35,0.7 factors on inertia in chapter 10 of ACI 318 for slenderness effects. 5. Also according to code, you can use the above same model in step 4 for lateral deflections. 6. Now for lateral deflections, if the lateral load is service (like Wind load of ASCE 7-05 and previous) multiply above factors by 1.43 or 1.40 (see code). For strength lateral load like Earthquake, no need to multiply by this factor. 7. Some times you really dont need to apply modifiers at all. For example for strength design. 8. For a two-way frame with membrane slabs at top, you just need to apply 0.5 factor to beam elements. Code allows this which says for strength design you can either a. use the same modifiers as used for slenderness b. use 0.5 for beam stems only In simple words, modifiers are factors to reduce inertia for cracked sections. But if you are doing strength design, why you need the cracked inertia. And as far as serviceability is concerned, authors like Nilson even argue that a factor of 0.5 as we applied in step 8 can also be skipped because of the following reasons. a. For positive moment, beam is designed as T section but in ETABS we use rectangular section, Stiffness of T = approx 2 x stiffness of rect. So no need to apply 0.5 inertia factor to beams because T compensates for that. Just use the rectangular section in ETABS. b. For negative moments, beam is designed as rectangular, and we also model the rectangular section in ETABS. Now the cracking in this section is offset by the continuation of bottom bars into support which have stiffening effect. I hope that helps. Let me put it as a summary here; 1. Strength & service design with membranes (slab on rigid beams as compared to slabs). Beams = 0.5 or beams = 0.35 & columns = 0.7 (or whatever ratios just keep it constant). or no modifiers at all walls = 0.7 for un-cracked 0.35 for cracked 2. Strength & service design with shells (flat plates etc). beams and walls same as above slabs = 0.25 for out-of-plane m factors. just multiply above factors by 1.43 for service lateral deflections.
-
i have done all the experiments before posting and the results are; we will get the same displacements if we 1. model a cantilever column with fixed support 2. model a shell element of same size with pinned supports (more than 1 support will act as fixed) and dividing total horizontal tip load as work equivalent load with poison ratio = 0. this is logical. now lets move on if we model a frame with columns as line elements, and then replace these columns with shell elements of same size with above assumptions in step 2 we will get different results. reason behind is the joint stiffness where beam frames into vertical elements. to get same results adjust the beam in shell models to the full length of shell elements (making joint more stiff). this is again logical now move to next step replicate these models for 10 stories, you will need to adjust the beams framing into shell elements to get the same results as that of multi-storey plane frame. go so forth now the problem lies when you actually model a 3d building...with line elements as columns, and then using shell elements as columns of same size. thats where im stuck.
- 21 replies
-
- column vs wall modelling
- shell vs frame
-
(and 2 more)
Tagged with:
-
I would not have posted if it was that simple..anyway...im exploring it...when i will get an answer ill update
- 21 replies
-
- column vs wall modelling
- shell vs frame
-
(and 2 more)
Tagged with: