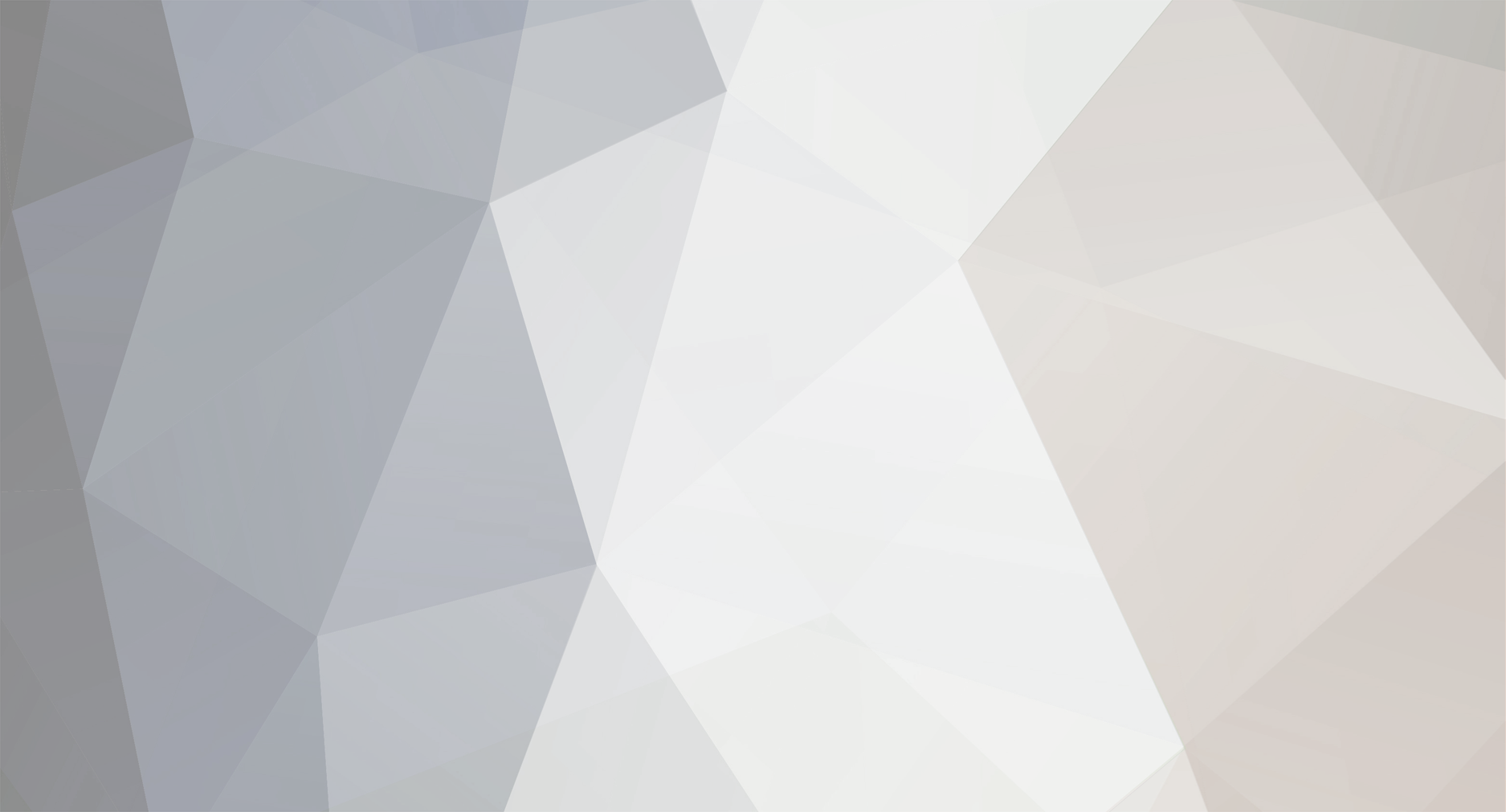
WR1
Administrator-
Posts
985 -
Joined
-
Last visited
-
Days Won
286
Content Type
Profiles
Forums
Events
Everything posted by WR1
-
I dont have any exp in PBD but here are my 2 cents. Please correct me if wrong. Performance based design is a nonlinear dynamic problem. By this we try to model post-yield ductility and energy dissipation for example under an earthquake. Ductility is very important in seismic design and ductility is actually a ratio of Nonlinear response / linear response This is handled by R factors in code. Again R factors are for all the modes of vibrations. Which in reality is not true. In linear elastic analysis we design structures for earthquakes for very small forces and actual EQ forces are quite large. But still structures desgined like this have performed well because the structure show a ductile behaviour which is very difficult to model from code based approach. So we assume the remaining portion of forces are handled by ductility. This ductility is handled by proper reinforcement detailing of members and joints. Where as in PBD as the name suggests we design based on performance of a structure. We try to model energy dissipation of structures. For example kinetic energy is applied to structure in an earthquake this is converted to elastic strain energy. Think of this as a car moving (it has kinetic energy) and then it hits a spring fixed on wall...This kinetic energy will be transferred to this spring and the spring will compress and it has now elastic strain energy. Now this SE must be dissipated from the spring otherwise it can react back to car and can throw its passengers outside. This energy dissipation in buildings is handled by damping (really difficult to predict) In buildings damping consists of 1. any external equipment like tuned dampers (liquid dampers, mass tuned dampers, braces etc) 2. Material inbuilt properties 3. Joints (e.g. beam column joints) We assume all above 3 to give around 1-5% of Critical damping. Critical damping is the damping where a structure vibrates and never crosses its mean position. Think of it as container filled with liquid and a spoon is immersed in it. Now the spoon will vibrate if external force is applied. Now increase the viscosity of the liquid in container and keep increasing to the point where the spoon vibrates from its mean position to left and comes back to its mean position and stops there (does not go to right). This viscosity of the liquid has critical damping Cc.(that's why we call it viscous damping/dampers). In buildings the damping is 1-5% of this Cc. In PBD we try to model these dampers.
-
Sefp Is Three Years Old
WR1 replied to UmarMakhzumi's topic in Website Announcements/ Problems/ Login/ Registration Issues
I would also like thank our most proactive users; and ofcourse the admin Sir Umar and very much respected senior Sir Baz waqar saleem baz EngrUzair Ayesha Waqas Haider abdul qadeer 06 asadishaq M.Naeem jammer3425 haro0n Nustian371 I would also like to thank our experienced user in high-rise; Muneeb Badr And finally I would like to thank EngUzair as his replies are always detailed that show his dedication and efforts for SePakistan -
Dear; If the deflection is excessive you need to increase tension steel (TOP) in cantilever. But if the deflection is less excessive you can reduce it by adding additional compression reinforcement (BOTTOM) in cantilever. What does it mean 1. Increasing compression reinforcement reduces long-term deflection (by small amounts) But it has very very minor effect on I-cracked (I-cracked almost stays same but Long Term Deflection decreases by little amount) 2. Increasing tension reinforcement reduces long-term deflection (by large amounts) But it has major impact on I-cracked (I-cracked increases and Long Term Deflection decreases by same amounts) So it is very clear that long-term deflection can be reduced by increasing I-cracked or in other words tension steel (TOP) in cantilever. But here arises one concern that if you change tension steel (so it will also change I-cracked) which in turn will change analysis and moment attraction. So you have to repeat the calculations. (Thats why we say to add compression reinf to reduce long-term deflection without analysing again). This holds true for continuous structure. For single span, you dont need to re-analyze. If you change I-cracked equally in continuous system you also dont need to reanalyze again. (Very rare). Conclusion If the deflection is huge (which is, i think) then increase tension steel in SAFE. (You can increase compression steel too but it will have very much less effect than tension steel). Hope that helps.
-
Sefp Is Three Years Old
WR1 replied to UmarMakhzumi's topic in Website Announcements/ Problems/ Login/ Registration Issues
Thanks sir umar and congrats for SEFP 3 years! -
Dear please make sure first that the minimum ratios you put are more than the source from FEM See SAFE help: Minimum Reinforcing Ratio Used for Cracking Analysis edit boxes. Minimum Reinforcing Ratio Used for Cracking Analysis edit box. Use this edit box to specify the minimum ratio to be applied to reinforcing during cracking analysis. This ratio applies regardless of the option selected for the source of the reinforcement specification (see three preceding bullet items). However, the program will use the largest minimum ratio. That is, if the minimum ratio specified here is lower than the ratio specified as part of any of the source options, the program will not use this value. So first check what is the reinforcement you are getting at strength level from FEM. May be it is more than T12@20cm which you are applying for cracking analysis. Please confirm this first!
-
New Column Dowels To Be Grouted Due To Wrong Layout????
WR1 replied to RASHEED's topic in Foundation Design
This is anchorage to concrete problem (i think, other please confirm) There are many industry post-installed anchors companies like Hilti which provide their own software to calculate these things. Check on Hilti website. -
If you will put on-site additional reinforcement only at bottom, then just do like what your engineer said (Tension=0.0095 and Compression=0.00256) If you are going to put additional reinforcement on both sides then put 0.0095 on both sides in SAFE. Having said that, you should know that compression (top) reinforcement helps reducing deflections. So put top reinforcement to control deflections.
-
Very well explained dear Muneeb!
- 7 replies
-
- energy dissipation
- aci 21.1.1
-
(and 1 more)
Tagged with:
-
In Linear analysis, forces and deformations are directly proportional to each other. For example axially loaded bar has extension equal to PL/AE...more P so more extension. This is linear analysis (inclined line in graph between P and delta). In non-linear analysis forces and deformations are not directly proportional. For example, even after removing load, strain continues to increase. There are three types of non-linearaties; 1. Geometric; for example p-delta (second order effects) structural stiffness can change as the structure deforms, and therefore the displacement will not be proportional to the applied load 2. Material; for example stress is not directly proportional to strain anymore after Hook's Law limit 3. Boundary conditions; contact between components depends on the load between the components, which in turn affects the stiffness of the contacting parts, and therefore produces a displacement response that is not proportional to the applied load. These 3 types of non-linear behavior can be studied in either A. Static domain or B. Dynamic domain One need to perform non-linear analysis if either of the above problem needs to be analysed and for those structures where one of the above 3 problems post sufficient doubt in linear analysis range.
-
Thanks Muneeb and you are warmly welcomed here. Put up a photo soon
-
Hi guys just to discuss with you my understanding of crack widths in Environmental structures according to ACI. --------------------------- Normal structures --------------------------- 1. ACI 318-95 based on statistical method of Gergely & Lutz 1968 limits Z based on exposure. We are calculating crack widths here. (Normal structures) 2. ACI 318-99 proposed limiting the spacing and removed actually calculating the width and also removed the exposure conditions. For example for beams and one-way slabs s (in) = 540/fs -2.5cc or in other words limiting the fs=0.6fy (For normal structures) 3. ACI 224R-01 references method 1 and 2 above and 3 european codes. The most confusing part is the table in which Nawy suggests 0.1mm crack width for water-tight structures. The whole document is for normal structures except this line. And people are following this line and refer to this document for water tight structures. I mean its just a suggestion and by the way this method 1 is obsolete now since ACI 318-99 (see point 2 above). --------------------------- Water tight structures --------------------------- 1. ACI 318-08 states clearly that for watertight structures ACI 350-06 codes should be used. 2. ACI 224.4R-13 also specifically states that for watertight structures walls in section 7.4, we should use ACI 350-06. 3. ACI 350-06 for water tight structures does not recommend calculating a number for crack width but rather limiting max steel stress in bars to be 20k ksi or fs=0.33fy for normal conditions. --------------------------------------------------------------------------------------------------------- To sum it up, Philosophy of crack width control is not to calculate probable crack widths but to limit the max stress in steel bars. For normal structures: fs=0.6fy and for water tight structures fs=0.33fy
-
PGA is the acceleration experienced by ground and SA is the acceleration experienced by building SA < PGA because foundations are not ideally fixed (rigid) they have some flexibility so less acceleration is transferred to the building.
-
I never designed structures for snow, but SNOW is included in load combinations of ASCE and ACI. So the apply the snow load and design on the governing load combination. I don't think there could be any other method. Yes, there could be different other ways, the way you calculate SNOW load but the overall philosophy is same.
-
Thanks Waqar, Thats very informative and comprehensive list. Keep up the good work!
- 2 replies
-
- Fyp
- Final year Project
-
(and 2 more)
Tagged with:
-
try making pattern live load factor to 0.
-
Are you sure, design results are from STRCOMBO2 (the same combination you are showing moments on) reinforcement is also affected by seismic detailing requirements. check in code what seismic category you are putting.
-
Without checking your model I would suggest that you check on which combination you are getting 4.5% reinforcement. Then check the moment diagram on that combination and make sure its okay! You can always make a simple 2d model of a frame to compare the results. It the column is at upper story, you will get more moment than axial force so e is more and so is the reinforcement.
-
Sameer yes you are right for slab extrusion below beam. In this case you will not apply end offset as = half slab thickness. But I was talking about a general concept. Anyway, sometimes it is necessary to change end offsets manually. But for most of the part in ETABS end offsets are okay. For example when a beam is rested on another beam end-offset is not properly calculated. I am not sure if it is the same in ETABS 2013 or not. I was talking in general for end-offsets. As I thought Junaid was talking about j end. But in this case Junaid, you dont need to change anything. You have to provide reinforcement at 0 location at i end. Thanks and it was a nice discussion btw. Hope this clarifies your concern Junaid?
-
1. ETABS will never design a column or beam inside end-offsets (NEVER!) You can do joint design manually by taking moment inside the joint but I am talking here about the column design specifically. 2. ETABS will design a column at 0 location in some cases. For example at foundation level. There is no framing so end-offset will be zero and design will be reported at 0.0 3. It is important to check the local axis 1-1 direction (red) in column to see which one is I end and which one is J end. As EngrUzair said,we should be sure if ETABS or any other software taking the input and output correctly or not. And Junaid, If you right click on C15 in your model, you will find out that end offset i = 0 (at floor level) and end offset j = 36inch (at soffit of beam). This is what sameersaleem was suggesting actually. so basically what ETABS is doing in your case is correct. It is reporting values at 0.00 that is your slab level. If you want to go a step ahead you can change the i end offset value = half of slab thickness because it is center to center modelling.
-
Welcome Kemal, Yes some of the areas in Pakistan are at higher risk regarding seismic activity and yes technically seismic design is properly understood and applied here in new buildings. As far as I am concerned, I use ETABS.
-
Uzair but if the end offsets are correct (either put manually or automatically at the soffit of slab) then there should be no reason to design column at 0.0 location.
-
First thing is why etabs is not taking end offsets automatically? end offset should be at the soffit of beam for the column design. if etabs is not taking it automatically you can assign it manually. No need for moment design at 0 location.
-
Opening Of Etabs2015 File By Version 9.7.4
WR1 replied to Aadelaadel Fd's topic in General Discussion
You can even use MS WORD for this! -
There is also an option to design composite sections in ETABS 2013 and 15. You can read ETABS composite design manual from help menu for more information. Or you can use CSi column to design composite sections.