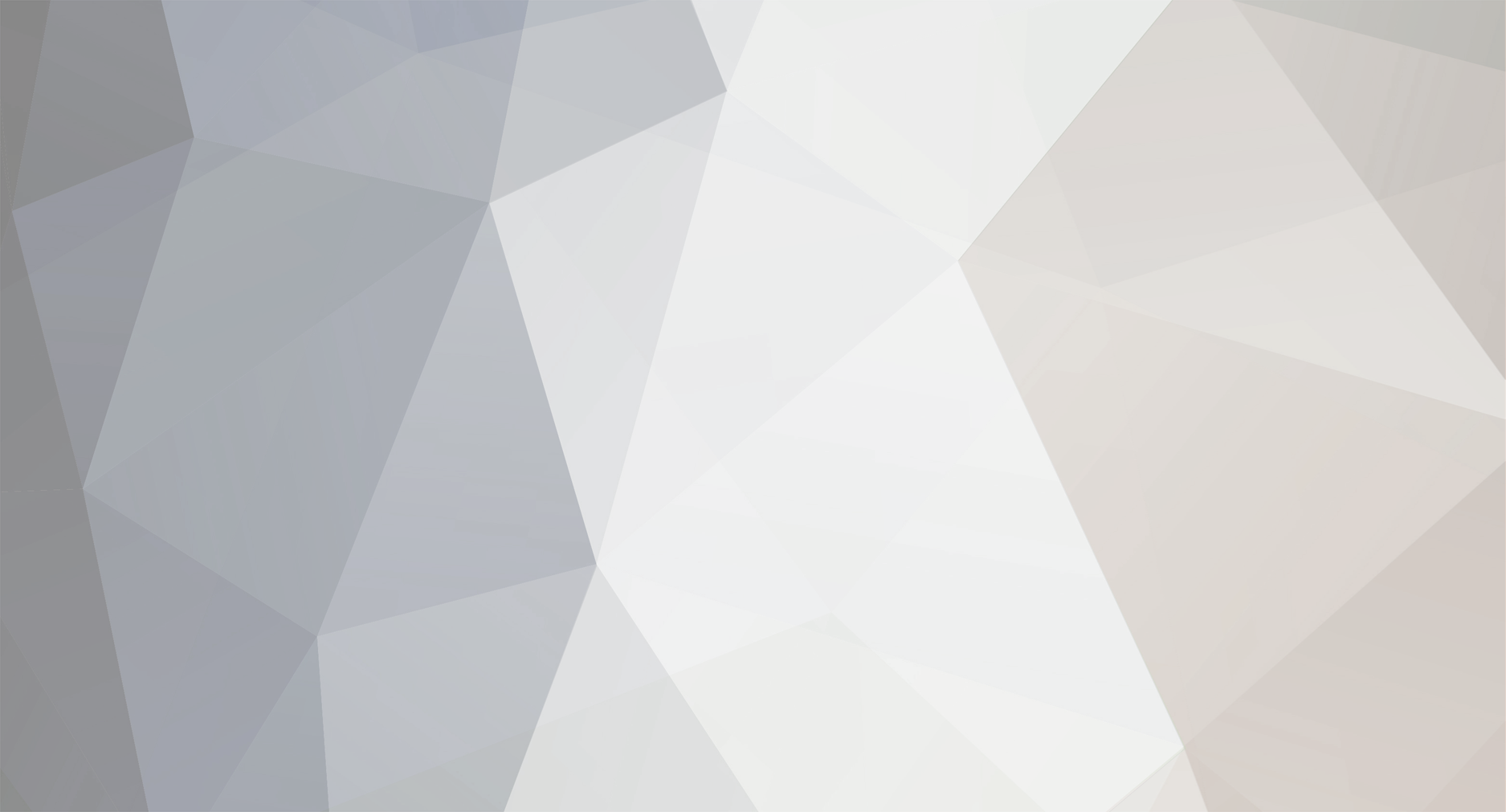
Nustian371
Member-
Posts
45 -
Joined
-
Last visited
-
Days Won
13
Content Type
Profiles
Forums
Events
Everything posted by Nustian371
-
Calculating Partition Wall Load on Slab
Nustian371 replied to Muhammad Munaf's topic in General Discussion
Normally you will find these Super dead load values in the design codes, which are given as area loading (kPa). check ASCE you will find it there. -
Will agree with the statement above but i think it all depends on the designer that what perfromance he wants from the structure based on that he can use the loading method. Mostly structures are best designed that they remain in elastic range so they become more ecnomical so ESM is recommended but as we have the means to do better analysis we should run RSA along with ESM to verify the results and behaviour of the structure to understand the force transfer mechanism and rotations. There are many varibale like ductility, displacement etc which defines the performance and also dictate the design method.
-
The procedure which we normally follow here for testing is schmidt hammer testing for the concrete strength and hiliti use rebar scanner for steel reinfrocement checks. This gives good idea. in case of critical structures where more precise info is required we hire testing companies for rebar scanning and exact size, shape and spacing. They do X-Ray testing, wave testing etc to verify the reinforcement and give us the results. the next step is IL4 structures like hospitals etc there if we donot have good information on the as built we might go for some core testing and break the plaster on walls to see the actua size of reo and even cut steel reo (only in case the building was built prior to 1920). The location of the steel sample is based on structural system, and normally the secondary or tertiary elements are used for this type of testing.
-
I would agree with this, as here in New Zealand we do quiet abig number of builidng and bridge assessments on frequent basis. Number one goal in doing an assessment is to get the as built information along with all the records of structure and do detailed inspection of the structure along with several tests for concrete and reinforecment scans at critical locations. Once you are comfortable with all the information you had you can start it any way by hand or using a software. If in case some info is missing you can discuss with th client the assumptions you are considering for your analysis based on the codes and design methods of that era.
-
If you are doing it for the first time i would recommend you do the PT design manually to understand the behaviour of the forces first as the stresses equivalisation in the slab is important. you can deal wth the column strips individually. The diaphragm reinforcement interaction with the PT alos needs to be looked in detail. So that the location of reinfrocement is right. u would suggest use PCI manual for the basic design. Maybe someone else give you a hint on ETABs but i belive if you are doing something new in software than there are alots of variable which you can comprehend in the first analysis. I hope it helps a little.
- 3 replies
-
- post-tensioned
- slab
-
(and 1 more)
Tagged with:
-
the best approach would be if you get it worked through pin connections. This will avoid lots of issues like moment at connections.
-
For the vehicle vibrations you have to look at the transportation design codes like AASHTO, NZTA Bridge Deisgn manual etc. We have to use the impact factor for the traffic live loads and braking forces on the concrete surface. the concept goes back to bridge design but as long as you check the concrete slabs and beams for the barking forces and impact loads the vibration is controlled. The structural diaphragm system is also important as the stiffness is controlled for the RC slabs. These all variables effect the vibration frequency of the slabs and concrete members. i know these are so many things to account for but you have to be specify the approach you are taking to solve the vibration issue.
- 10 replies
-
- floor vibrations
- vibrations
-
(and 1 more)
Tagged with:
-
I am working with Austrailian/New Zealand codes. (AS/NZS 1170). the vibrations come under the serviceablilty requirements. If you see the table attached we use 3kN superimposed load for the design check which reduced by 0.5times for the service check for the beam vibrations. AS/NZS 1170 says that minimum 1kN load should be checked for vibration with 1 to 2mm deflection under the point load but we use 1.5kN minimum. have a read on the attached as they are self explainatory.
- 10 replies
-
- floor vibrations
- vibrations
-
(and 1 more)
Tagged with:
-
Hi Usman, Good to see you here. Just to let you know i have done my masters from Bauhaus and its a great institute. Donot miss the summer school as lots of engineers from around the world come and share there knowledge and experience in seismic design and perfromance based design. Gud luck
-
11PSF looks very light to me i am using metric units and we commonly use 1.5kPa to 2 kPa superimposed loads for the calcualtion (1.5KPa minimum) of the floor vibrations. U have to take care of the live load as well as pedestiran traffic on the floor.
- 10 replies
-
- floor vibrations
- vibrations
-
(and 1 more)
Tagged with:
-
Normally you do the frequency analysis for the composite floors. It depends on the length of beams and associated deflection allowed.
- 10 replies
-
- floor vibrations
- vibrations
-
(and 1 more)
Tagged with:
-
I will add some more, once you are working out the forces within the tank you have to find out the impuslive forces due to seismic action and the height of the mass above the base of steel tank. You can work out the moments against that moment arm for the concrete structure and at the base slab. Just corss check the forces against the hoop tension generated in case of a circular tank.
-
Damping of structure after Pushover analysis
Nustian371 replied to Nustian371's topic in Software Issues
yes sir g, the word structure means complete structure along with the dampers. I have calculated the dampers as 10 to 11% damping and assuming that we can achieve the damping of structural steel as 3% to go close to 14 to 15 % system damping. But the question is , Is there any way that you can check this in ETABS model at the end of analysis rather than calcualting from the damper properties or the supplier values. we just want to make sure taht what we assume we tune our sturture to that damping and workout the forces based on that. Excuse me for late replying. Just for refernce i have attached the model snapshot and damper i am using. RSFJ Structural Modelling_04.18.pdf -
Damping of structure after Pushover analysis
Nustian371 replied to Nustian371's topic in Software Issues
hi Sir g, You are almost there, I will try to reitrate the question, i am after the overall system damping generated after the analysis. Is there anyway we can check it from the model itself using the damper properties calculated from the ESM. we have generated an excel sheet to calculate the flag shape hysterisis loop for the dampers in case of cyclic loading(seismic) and calculate the individual damper damping in that. But i am after the damping of the structure generated by using the dampers. As you know the structural damping will be not same as 5% which we assume initially for a ductile structure. Thanks, -
Hi All, Please if someone can guide me how to claculate the overall structural damping after doing the pushover analysis in etabs using linear frictional dampers. I have a case in which i am designing the dampers. I am defining the forces etc in the etabs regardless of initial damping to get the required response of the structure in after the ULS seismic event. NOw the question is to calculate back the damping generated by the system using the link properties i defined. Just any start up hint would be great. thanks. Regards,
-
I Would like to know that you have designed your column end plate as moment resisting connection with two layer of bolts then why you need to weld our beam to the column. It is very difficult on site and as per my experience I have never seen to types of connection at one end. Thanks
- 7 replies
-
- steel
- connection
-
(and 1 more)
Tagged with:
-
For the design of flange brace you need to check the restraints strength of the member as per your code limits. Based on the restraint length you can get the force required to design your brace. Sir Umer and sir Zeeshan correct me if I am wrong. Thanks,
-
With connections design you have to be very careful. As you mentioned one end is going to be hinged and other will be roller, Your truss on each side will have a certain width and it wont be resting with one support connection. I mean at each end the truss will have two or three connection points with the beam or corbel. So when you say hinged it be virtually not hinged and will become a kind of fix connection as the number of anchor bolts on each point will be bore than two. So check your building movements in worst cases, like seismic and wind etc and design the slotted hole connections by giving appropriate movement at the joint. For the roller connection you will use the rubber pads any type but you must make vertical pins through sleeves on corbel beam or any connection through your bridge to restrict the dislocation of your truss form the pad. Normally the rubber pads come with these pins and slotted holes are provided in the truss base plates which help them to restrict movements. See Granor Rubber Pad bearings for bridges. I have attached two examples of what I have said above. I hope they make any sense to you. Bridge Connection.pdf
-
Hi Waqar, I hope you have got your answer from sir Umer and others I will just add something as per my experience with the steel structures. In most cases cold form steel or light gauge structural members are designed on the basis of local failure in stead of global. These buildings are single storey most commonly and double to triple storey in very special cases. So the loadings are worked out manually and each member either column or beam/truss is checked for the local buckling and bending, axial and shear stresses. These members can be modelled individually in SAP 2000. The members are closely spaced to each other like wall panels may have studs at every 400mm c/c and then for door jambs and window head your section are doubled etc. So the steel in a wall section or roof members is quiet high. For the modelling of these structures you must do these manual checks before and calculate the required capacities of each members and your required bracings etc. then you model the structure you will get the results. But still having said that the wall studs have many jointing elements like horizontal support members for the installation which are normally difficult to model and these restraining elements also help in reducing the KL/r for the elements. which is not considered in most cases during modelling. So the best is to do these structures manually and verify them by any software with logical assumptions. software like framecad are designed for these structures so they take into effect all the restraints as you build your 3d they add all the required horizontal supports due to which the analysis results are different to as modelled in SAP 2000. Cheers,
-
I will try to be active in steel section from now on...