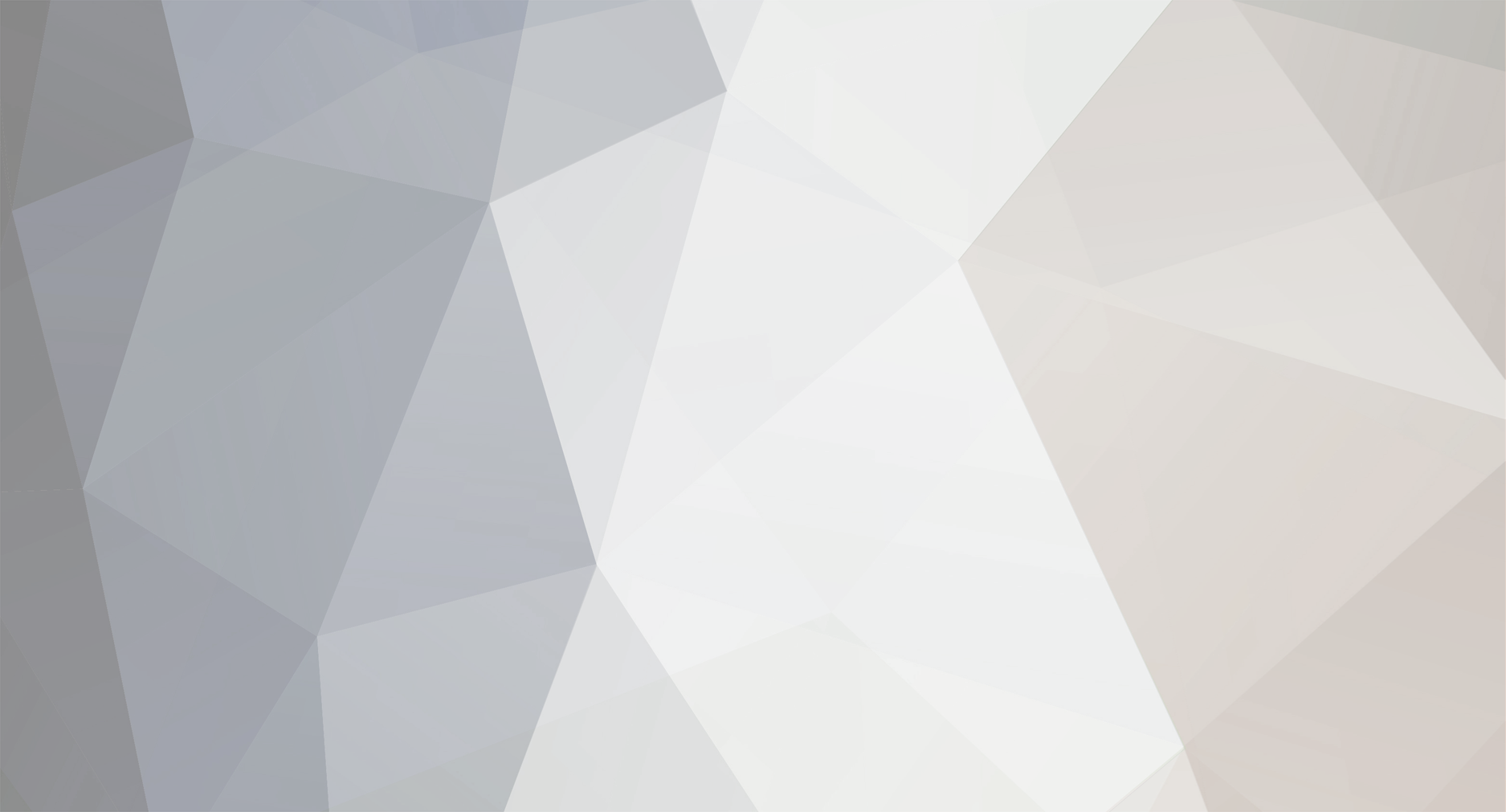
Dik
Member-
Posts
45 -
Joined
-
Last visited
-
Days Won
5
Content Type
Profiles
Forums
Events
Everything posted by Dik
-
Point of minimum moment is likely about mid height of the column; it's not generally convenient to splice at that level.
-
Partition Load calculation (Effective Method)
Dik replied to Muhammad Sohail Hussain's topic in General Discussion
I do that occasionally, else we have a prescribed partition load. If you base it on actual calculations, you have to stipulate this and that partition layout cannot be changed except yby a prof engineer. In addition. When it comes to actual calculation of partition loads, make sure you subtract the design floor live load for the area taken by the partitions. dik -
I'm not sure what a lap zone is... is this a splice location? If so, in these environs, splices generally occur at finished floor level in multi storey concrete buildings. For steel buildings I put them about 2' (600mm) above finished floor.
-
He's unable to comment; he cannot determine the cause. Back to 'trial and error'.
-
Thanks... will see if I get any info back; I was waiting for approval.
-
I'm not a materials guy, but can I share this with someone that is. He may be able to offer a suggestion.
-
Ignore... I misunderstood your reply Limited... but glad to help... you're coming into your summer and we are starting our winter. For the different types, the first column is the cement type (General Use Portland Cement that may be blended) The second column is the strength in MPa, The third column is the aggregate size, the fourth column is the slump and the fifth column is the air entrainment. I'll try do dig up some info on CLSM; this is a mix design for ultra low concrete strength used for fill or backfill against walls to minimise lateral loads, etc. The trial mix proportions are from my drawing notes for specifying it.
-
Tayloring mix designs is a complicated task. Even readymix suppliers sometimes have difficulties preparing a batch, and there may be a lot of trial and error in preparing a mix. You might reach out to someone that specialises in this work and see if they can provide some guidance.
-
You may have to try a couple of batches to get the right mix. If you have a readymix supplier, they may be able to help (maybe not if you are a readymix supplier). There may be a concrete lab in your area that may be able to assist. I ran into some hiccups about 50 years back when I inadvertently specified some CMUs that were about 1000 psi above normal (out of ignorance) but they were able do provide the material.
-
What are the issues? and lightweight mortar, or concrete masonry units? I've not encountered lightweight mortar.
-
I've attached a file with HC details from the past. I do not recall the source. They are in AutoCAD/Bricscad *.dwg format. I couldn't find the ones I drew up... it's been nearly 30 years since I've used them. I've done nearly 20 storey high HC with concrete masonry unit buildings as well as reinforced concrete. It's common construction in these areas. Load bearing brick is not common, here. I've never used Staad... Hollow Core.7z Cv_dik_23-02-20.pdf
-
I don't know where the negative comes from, but torsional shear occurs when a rectangular concrete beam is subject to torsion. It's the shearing force in the concrete caused by the reaction to the torisonal load. Most current codes address this. Depending on the torsion, the stresses can be fairly high. The stresses are in addition to those caused by actual shear. When I first started engineering, other than the Russians, there was very little information about the design for this. The ACI at the time only had a reference that this had to be addressed. I did my thesis on propagation of cracking in torsionally loaded beams.
-
Can you cast a 'hairpin' into the masonry wall at the hollowcore joint locations and use a 180deg hooked bar grouted into the hollowcore joint? or even hook the 180 bar around vertical steel in the wall?
-
Can I get you to re-send the canopy files?
-
Then you likely have to do a preliminary design of the canopy to determine what shears and moments are created. In addition, you have to clearly stipulate what your design criteria is for the canopy designer and fabricator, so he ends up with similar. You also have to stipulate on your drawings what your design loads and resulting reactions (that includes +ve and -ve forces) and leave the final design with a condition that the canopy loads cannot exceed your loading criteriia, and that you are not responsible for any redesign costs. It's a bad way to do it. It's difficult in assigning someone the loading; I hope you have some control over it. Why would the regulatory authority have any input as to the type of construction. HSS columns with proper anchors is a much better way to go. If the column has to be concrete, it might be better to construct it once you have the canopy loading, and put the excess design into the foundations. Foundation costs are relatively insensitive to loading (usually). Dik
-
Can you hold off on the column design until you have design loads for the canopy? Also, can your columns be steel rather than concrete? HSS material makes good columns, and is easy to connect to concrete foundations as well as a steel canopy.
-
I'd likely try to develop two separate lateral load resisting elements in 'both halves' of the structure and isolate the connection at the top. How are the lateral loads resisted? What is the height? and what is the approximate height from floor to floor?
-
I assume wind is the issue... in these environs it is wind and snow. You may find this informative:1-Wind_Loading_on_Attached_Canopies_A_Codification_Study.pdf
-
Great article. In these environs, the top 10' (3m) is excluded for exterior piles for desiccation as well as frost, and 5' (1.5m) or so for interior piles, for the same reason. The pile lengths would be reduced to that required for the load capacity. If you have different loads, they would try to maintain the same diameter for the pile and change length to accommodate loading rather than change pile diameters. It's less costly in this area to keep the same size pile. For a 12" (300mm) pile, reinforcing would typically be a single 15M deformed bar in the centre. "Pile caps are designed as slabs." They used to be designed as beams... current trend over the last couple of decades is to design them using 'Strut and Tie' methods. LPile is a common program in this area; I've not used it. It has a good reputation. I have several programs written in SMath to help me for axial loading and lateral loading, and use P-M concrete column design for checking for piles with moments.
- 10 replies
-
- sefp consistent design
- piles
-
(and 1 more)
Tagged with:
-
Were thermocouples ever used for this project to determine the temperature differentials?
-
First choice due to the high strength requiring lots of cement paste.
-
Could the issue be plastic shrinkage cracking? https://www.sciencedirect.com/topics/engineering/plastic-shrinkage
-
If leakage is a serious problem then a waterproof membrane is nearly always prescribed. If a little leakage is OK, then you might consider a perimeter drainage system around the tank and sump pit .
-
How far below grade is it founded? How thick is it? Can the UGWT be built into the raft foundation. Can it be expanded in size to minimise the depth and the loads on the tank walls?